Crystallization
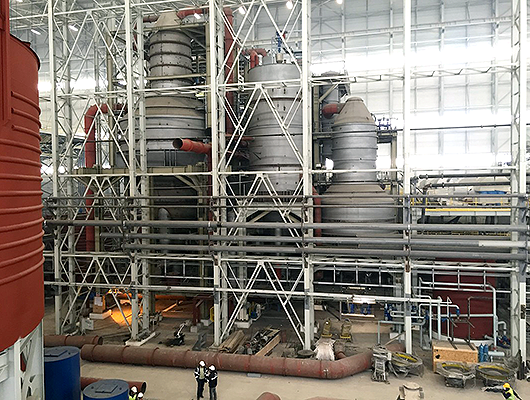
France Evaporation has developed complete expertise of crystallization technologies applied to many industrial processes such as the production of chemicals and pharmaceuticals, upgrading mining by-products, treatment of cheap wine, recycling, etc.
This expertise has led to several technologies being developed in our laboratories and pilot units whose IFC® technology is a real innovation in the sector.
Size and homogeneity of crystals, energy efficiency, total cost, robustness: our technological solutions adapt to any type of industrial purpose and within the quality and budget imposed limits.
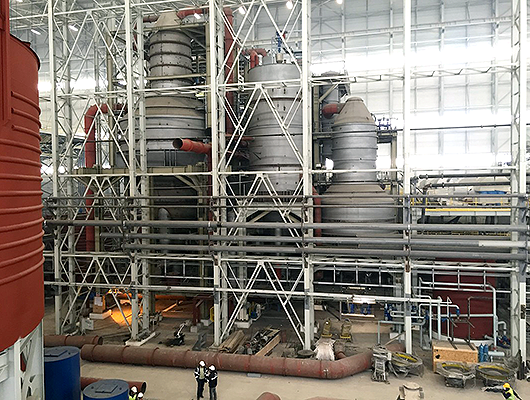
France Evaporation has developed complete expertise of crystallization technologies applied to many industrial processes such as the production of chemicals and pharmaceuticals, upgrading mining by-products, treatment of cheap wine, recycling, etc.
This expertise has led to several technologies being developed in our laboratories and pilot units whose IFC® technology is a real innovation in the sector.
Size and homogeneity of crystals, energy efficiency, total cost, robustness: our technological solutions adapt to any type of industrial purpose and within the quality and budget imposed limits.
Crystallization technologies
Crystal clear solutions
IFC®: The new generation of high performance crystallizers
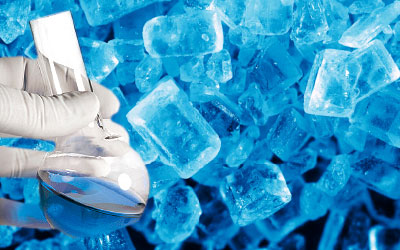
2015 innovation:
Discover the exclusive IFC® technology
Larger size
Narrower distribution
- Chemical
- Salts and Mines
- Fertilizers
- Food Industry
- Water and Waste Management
- Pharmaceutical & Cosmetics
Safer and more sustainable
The IFC® technology avoids contacts between crystals and pumps or agitators built into the crystallizer without reducing or altering their circulation. At stake: a very significant reduction in the rate of failure and very streamlined maintenance transactions.
IFC® specifically meets the needs of markets:
- average size of larger crystals
- better distribution of size
Crystals with larger sizes for maximum upgrading
IFC® ensures an average crystal size (D50) greater than that obtained by a crystallizer.
A high quality production through an excellent distribution of crystal size
The size distribution of the crystals obtained by crystallizing IFC® is close to the average size, the amount of fine is greatly reduced compared to other crystallization technologies.
The IFC® design allows a better control of secondary germination.
As such, the IFC® crystallizers guarantee a very high quality production, regular and simpler to develop in markets including the most demanding (pharmaceuticals, Chemicals, etc.).
A production of very reduced fine
IFC® produces less fines than other technologies in the market, from fines drying output is reduced. Typically, it is less than 3% against 10% for other technologies.
Energy efficiency
The IFC® technology provides crystal sizes equivalent or even higher to those produced by DTB crystallizer, but with a much lower energy consumption, in the case of a MVC / RMV unit.
IFC® in action
Several IFC® crystallizers were designed and launched in 2011.
- For the production of Na2SO4, installation performances reach a d50 greater than 400μm (against a d50 of 250µm on other technologies).
More informations
- For the production of (NH4) 2SO4, the IFC® technology allows to obtain crystals with a d50 greater than 2 mm and a crystal distribution of 25%.
More informations
Brochure
This fluidised bed crystalliser has a very large volume and provides large crystals, greater than 2 mm.
The crystals are fluidised at the bottom of the crystallizer using an external axial pump which contains the mother liquor in the upper part and resends them to the crystallizer.
The residence time may exceed 10 hours.
However, this powerful technology requires frequent cleaning.
The drill pipe crystallisers (DT and DTB) ensure the homogeneous mixture of the crystals in the crystallizer with an internal axial pump.
The energy provided by the pump is lesser than that deployed by a forced circulation, which significantly reduces attrition and breaking of crystals.
Crystal size may be greater than 2 mm and the residence time greater than 10 hours.
A surrounding decantation zone is often added to remove the fines and thereby increase the average size of the crystals.
Often used for relatively low flow rates, the method is not continuous but run in batch.
France Evaporation develops production processes on this technology and also more sophisticated units for research or tests on lower volumes.
The homogeneous mixture of crystals in the crystallizer is circulated by an external pump.
Minimum investment
Due to its simple design, the investment and working costs are greatly reduced. Small compared to other technologies, this crystallizer is easy to implement and reduces the costs of huge projects.
Simplicity of transaction
Simple and robust design, this crystallizer allows an easy conduct to the detriment of the quality of the crystals.
Crystal size
The substantial contact between the crystals and the pump limits the growth of the former.
The residence time is limited to a few hours because the effects of crystal attrition become so prominent in growth rate.
Applications
This type of crystallizer is very suitable for production without grain size constraints.
Used in many industries, forced circulation is also used in the ZLD (Zero Liquid discharge) units.