Cristallisation
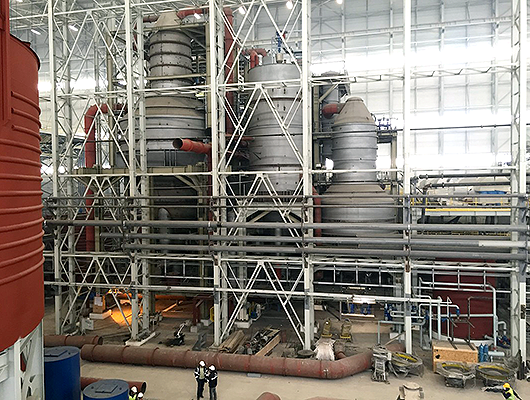
France Evaporation a développé une expertise complète des technologies de cristallisation appliquées à de nombreux process industriels : production de composés chimiques et pharmaceutiques, valorisation de co-produits miniers, traitements de vinasses, recyclage, etc.
Cette expertise a donné naissance à plusieurs technologies mises au point dans nos laboratoires et unités pilotes, dont la technologie IFC®, véritable innovation dans le secteur.
Taille et homogénéité des cristaux, efficacité énergétique, coût global, robustesse : nos solutions technologiques s'adaptent à tout type d'objectif industriel et dans les limites imposées de qualité et de budget.
Télécharger la brochure2.44 MB
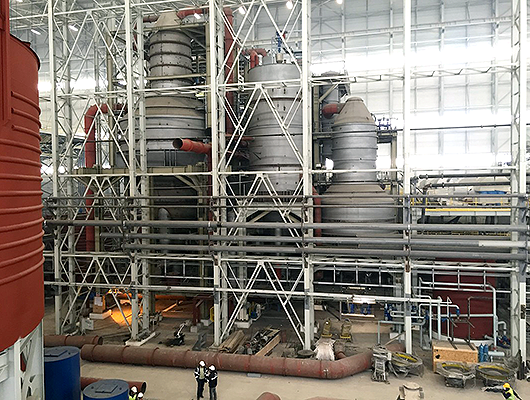
France Evaporation a développé une expertise complète des technologies de cristallisation appliquées à de nombreux process industriels : production de composés chimiques et pharmaceutiques, valorisation de co-produits miniers, traitements de vinasses, recyclage, etc.
Cette expertise a donné naissance à plusieurs technologies mises au point dans nos laboratoires et unités pilotes, dont la technologie IFC®, véritable innovation dans le secteur.
Taille et homogénéité des cristaux, efficacité énergétique, coût global, robustesse : nos solutions technologiques s'adaptent à tout type d'objectif industriel et dans les limites imposées de qualité et de budget.
Télécharger la brochure2.44 MB
Technologies de cristallisations :
Crystal clear solutions
IFC® : la nouvelle génération de cristalliseurs haute performance
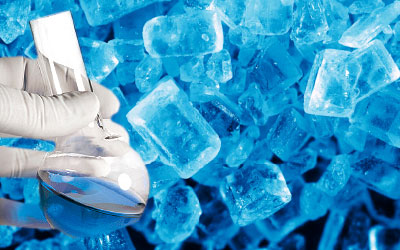
Innovation 2015 :
Découvrez notre technologie exclusive IFC®
Taille des cristaux plus importantes
Distribution plus resserrée
- Chimie
- Sels et mines
- Engrais
- Agro-alimentaire
- Traitement de l'eau et des déchets
- Pharmacie et cosmétique
Plus sûre et plus durable
La technologie IFC® évite les contacts entre les cristaux et les pompes ou agitateurs intégrés au cristallisoir, sans réduire ou altérer leur circulation. A la clé : une réduction très sensible du taux de panne et des opérations de maintenance très allégées.
IFC® répond particulièrement aux besoins des marchés :
- taille moyenne des cristaux plus importante
- meilleure répartition de taille
Des cristaux de taille plus importante, pour une valorisation maximale
IFC® assure une taille moyenne des cristaux (D50) supérieure à celle obtenue par un cristallisoir.
Une grande qualité de production, grâce à une excellente distribution de la taille des cristaux
La distribution de la taille des cristaux obtenue par les cristallisoirs IFC® est proche de la taille moyenne, la quantité de fines est fortement réduite comparativement aux autres technologies de cristallisation.
La conception de IFC® permet un meilleur contrôle de la germination secondaire.
Les cristallisoirs IFC® garantissent ainsi une production de très haute qualité, régulière et plus facile à valoriser sur les marchés, y compris les plus exigeants (pharmacie, chimie, etc.).
Une production de fines très réduite
IFC® produit moins de fines que les autres technologies présentent sur le marché, la part de fines en sortie de séchage est réduite. Typiquement elle est inférieure à 3 % contre 10 % pour les autres technologies.
Efficacité énergétique
La technologie IFC® permet d'obtenir des tailles de cristaux équivalentes voire supérieures à celles produites par les cristallisoirs DTB, mais avec une consommation énergétique beaucoup plus faible, dans le cas d'une unité en CMV/RMV.
IFC® en action
Plusieurs cristallisoirs IFC® ont été conçus et démarrés en 2011.
- Pour une production de Na2SO4, les performances de l'installation atteignent un d50 supérieur à 400µm (contre un d50 de 250µm sur d’autres technologies).
Plus d'infos
- Pour une production de (NH4)2SO4, la technologie IFC® permet d’obtenir des cristaux avec un d50 supérieur à 2 mm et une distribution de cristaux de 25%.
Plus d'infos
Brochure de présentation : Indirect Forced Circulation IFC®
Ce cristallisoir à lit fluidifié, de très gros volume, permet d'obtenir des cristaux de taille importante, supérieure à 2 mm.
La fluidification des cristaux au fond du cristallisoir se fait à l’aide d’une pompe axiale extérieure qui reprend les eaux mères en partie supérieure et les renvoie dans le cristallisoir.
Le temps de séjour peut excéder 10 heures.
Cette technologie de cristallisation performante nécessite cependant un nettoyage fréquent.
Les cristallisoirs à tube de tirage (DT et DTB) assurent le mélange homogène des cristaux dans le cristallisoir par une pompe axiale interne.
L’énergie fournie par la pompe est très inférieure à celle déployée par la circulation forcée, ce qui réduit significativement l’attrition et la casse des cristaux.
La taille des cristaux peut être supérieure à 2 mm et les temps de séjour supérieurs à 10 heures.
Une zone de décantation périphérique est souvent ajoutée, pour retirer les fines et ainsi augmenter la taille moyenne des cristaux.
Dans le process de circulation forcée, le mélange homogène de cristaux dans le cristallisoir est mis en circulation par une pompe extérieure.
Investissement minimum
De par sa simplicité de conception, le coût d'investissement et d'exploitation est fortement réduit. De plus faibles dimensions comparé aux autres technologies, ce type de cristallisoir s'implante facilement et limite les coûts de gros œuvre.
Simplicité d'exploitation
Conception simple et robuste, les cristallisoirs à circulation forcée permettent une conduite aisée au détriment de la qualité des cristaux.
Taille de cristaux
Le contact important entre les cristaux et la pompe limite la croissance des cristaux.
Le temps de séjour est limité à quelques heures car les effets de l’attrition des cristaux deviennent alors prépondérants sur la vitesse de croissance.
Applications
Les cristallisoirs à circulation forcée sont donc très adaptés aux productions sans contrainte de granulométrie.
Utilisée dans de nombreux secteurs d’activité, la circulation forcée est aussi employée dans les unités de ZLD (Zero liquid discharge)
Souvent utilisée pour des débits relativement faibles, la technologie du réacteur agité n’est pas continue mais lancée en batch.
France Evaporation développe des process de production sur cette technologie mais aussi des unités plus sophistiquées, destinées à la recherche ou aux tests, sur de plus faibles volumes.